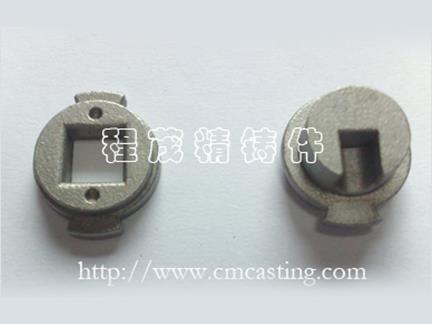
Lock hardware castings
Aluminum pressurePrecision cast steelIt plays an important role in the current industry, and has a very wide range of uses in many industries. The society is constantly developing, and people’s living needs are getting higher and higher. The demand for aluminum die casting technology is also increasing during operation. In the constant increase.
The main advantages of aluminum die castings
1. Aluminum die-casting parts are beautiful in appearance and light in weight, and can be easily transported during operation. It is also a great advantage to use in automobiles.
2. The density of aluminum alloy is obviously lower than that of cast iron, cast steel, etc., but it is much higher in strength and corrosion resistance. Therefore, under the same load and weight, the use of aluminum die-casting can greatly reduce the structural weight.
3. For the surface of aluminum alloy material, its surface gloss is very good, and it also performs well in casting performance.
Aluminum pressureLost wax castingThe mechanical properties and tensile strength of the parts are large when the material is broken during the production. To a certain extent, its elongation is a measure of the brittleness and plasticity of the material. The hardness is the pressing of the hard object on the surface of the material. Or resistance to plastic deformation caused by friction.
The working temperature and humidity of aluminum die-casting parts, and the requirements of the medium in contact with the workpiece, the accuracy and dimensional stability required by the entire product.
Aluminum pressureCoffee machine castingsThe accuracy of the profile and the surface roughness to a certain extent will directly affect the working efficiency of its pump and hydraulic system, energy consumption and the development of cavitation, etc., internal combustion engine cylinder block, cylinder head, cylinder liner, piston ring, exhaust The strength and heat resistance of cast aluminum parts such as pipes directly affect the working life of the engine.
Sand casting is preferred for aluminum die castings, mainly because sand casting has lower cost than other casting methods, simple production process, and short production cycle. When the wet type cannot meet the requirements, consider using the clay sand surface dry sand type, dry sand type or other sand types. The casting method of aluminum castings should be compatible with the production batch. Low-pressure casting, die casting, centrifugal casting and other casting methods are only suitable for mass production because of the high prices of equipment and molds. Cast aluminum parts can be cast in a single piece or can be mass produced.