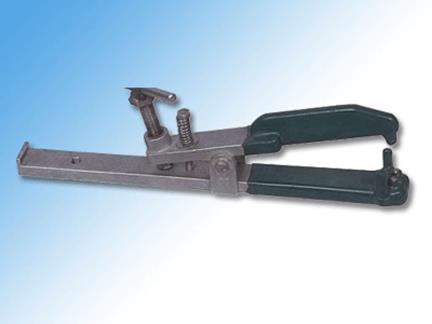
Electroplating hanger
The structure of the electroplating hanger is generally relatively simple, consisting of five parts: hook, lifting rod, main rod, support rod and hook.
The hook is the connecting structure between the hanger and the pole. It transmits current to the hanger and parts during electroplating. Therefore, it must be made of materials with good conductivity. The hook and the pole should maintain a large contact surface and good contact state to ensure smooth current flow. Its cross-sectional area is equivalent to the cross-sectional area of the same material of the main pole of the hanger. The hook must bear all the quality of the hanger and the plated parts, so sufficient mechanical strength is required.Lost wax castingThe hook and the main pole are usually made of the same material, and the two can be made into one body or made separately. Connect it to the pole by brazing or other methods and the hanger. For hangers made of steel or aluminum alloy, copper and brass are generally used for hooks, and the connection methods can be riveted and welded. Its size should be designed according to the diameter of the cathode rod, so that the hanger is easy to operate when hanging and removing.
The lifting rod is located on the upper part of the main rod and is perpendicular to the main rod, and is connected to the main rod by welding. When the hanger is hung in the plating tank, the position of the lifting rod should be about 80 mm above the liquid level. Use the lifting rod to extract the hanger during operation. It should have sufficient mechanical strength, and the cross-sectional area is generally the same as or slightly larger than that of the support rod. The main pole supports the weight of the entire hanger and the hanging parts, and transmits current to each support pole and parts through the main pole. The material of the main rod is generally a brass rod of φ(6~8)mm. The support rod is usually fixed on the main rod by welding, and bears the weight of the suspended parts during work. The material of the support rod is generally φ(4~6)mm brass rod.
Hooks are generally welded to the support rod, and sometimes also welded to the main rod to hang or clamp parts. The material is generally steel wire, phosphor bronze wire.
The distribution density of the hooks on the hanger should be appropriate.Guangdong alloy steel castingIt is necessary to make most of the surface or important surface of the parts on the hanger face the anode, and avoid the phenomenon of overlap. Generally, the interval between small and medium-sized plating parts is (15-30) mm, and the interval between cup-shaped plating parts is generally 1.5 times the diameter. According to the different connection methods of the hook and the plated parts, the hook can be divided into two types: hanging type and clamping type.
(1) Hanging hook. Plated parts and hooks generally adopt the free hanging method. That is, the hook is hung in the hole of the part or in an appropriate position, the part can be moved without falling off after being hung, and the contact point can be changed when the hanger is shaken. This kind of hook is convenient to assemble and disassemble, and the imprint of the hanger on the plated part is not obvious. When the current density is small in electroplating, the free suspension method is generally used.
(2) Clamping hook.Guangdong carbon steel castingThe connection between the plated part and the hook depends on elastic contact. Generally used in bright electroplating, chrome plating and other occasions or when using higher current density. It uses the elasticity of the hook to clamp a certain part of the part, and relies on the contact pressure to make it conductive. The strength of elasticity is determined by the material, wire diameter, wire length, board width and board thickness of the hook.
No matter which method is used to suspend the parts, it is necessary to ensure that the gas generated during the electroplating of the parts is smoothly discharged, so as to prevent the gas generated from accumulating in a certain part to form an "air bag" and affecting the quality of the coating. For example, when parts with blind holes and concave shapes are suspended, their mouths should be slightly inclined upward, and plastic parts should use multiple contacts to contact the hooks. In short, the form of the hook and the way of suspension depend on the shape of the parts and the conditions of the electroplating process.